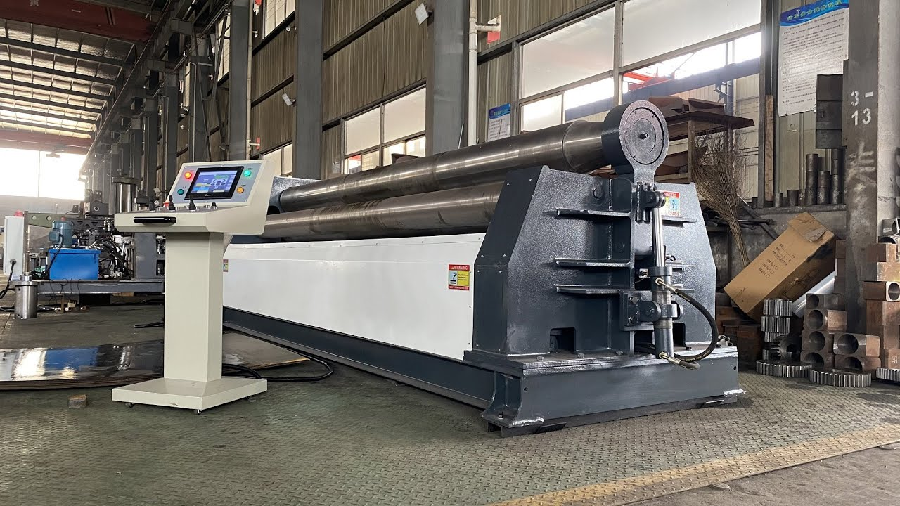
In Houston, Texas, extrusion, press braking, and stamping are less flexible, responsive, and cost-effective than roll forming.
Roll forming is a straightforward procedure that is excellent for even the most complex shapes. It is well-suited for bespoke or standard shape production.
Custom Metal Plate Rolling houston tx is a tried-and-true method of shaping metal appropriate for modern applications.
Long metal strips, commonly coiled steel, are passed through successive sets of rolls at room temperature, which involves a continuous bending operation.
The Process of Roll Formation
In Houston, every roll forming manufacturer has a particular set of stages for the roll forming process. Regardless of the differences, all producers follow a set of steps.
The process starts with a big coil of sheet metal, which can be anything from 1 inch to 30 inches broad and 0.012 inches to 0.2 inches thick. A coil must first be prepped for loading before it can be loaded.
The roll manufacturing operation consists of the following steps:
Uncoiling
- Metal coils tend to become fixed during storage and stay coiled and deformed.
- The coil is mounted onto the uncoiler and passed through a flattener to eliminate the coil set, satisfying the requirements.
- The lead edge is cut to ensure seamless insertion into the pre-press stage.
- The beginning of the feed coil may be tapered as part of the pre-press operations to make it simpler to slip into the molding rollers.
Pre-Press Treatment:
- Before metal from the coil is pushed into the roll-forming rollers, it will need modifications such as slots, perforations, or slits.
Cutoff and Discharge:
- Parts are trimmed to length while in movement, increasing the roll forming process’ performance and effectiveness.
- They are unloaded to a run-out bench after being cut and arranged for transport or additional processing.
Not Every Rolled Metal is Made the Same
Plate rolling is a critical component of a complex process in the Custom Metal Plate Rolling houston tx industry. It’s a science, too.
Although most rolled metal has minor faults and surface blemishes due to metal impurities, skilled machine operators can turn practically any metal plate into highly functional parts that meet or surpass your expectations.
Optimal plate rolling results necessitate:
- Roll operators with a great deal of experience
Skilled professionals should thoroughly understand metals, rolling procedures, and preventive measures to avoid mishaps.
Decades of industry working experience with crews of fabricators in a cooperative effort for achievement have given them this skill level.
- Industry’s top-of-the-line machinery
When looking for a metal fabricator for a project, find out about their machine competencies and how efficient these machines are just for the job that needs to be done.
Machines aren’t all made equal. This is also true when it comes to metal rolling.
Compared with similar instruments, in Houston Texas, some technologies, such as Parmigiani’s 4-Roll Bending Machinery, operate at a better consistency.
Conclusion
Metal rolling is, in fact, one of the most crucial procedures in metal manufacturing.
Serious faults such as fissures, voids, ripples, or warping can occur if it isn’t done to the greatest of specifications. Furthermore, this can compromise any finished architecture’s entire structural stability and reliability.
You rely on your end goods to be fully functional, safe, and trustworthy every time, whether the project entails steel beams, agricultural silos, roller coaster tracks, or anything in between.
Any potential responsibility resulting from faulty metalwork is indeed not worth the gamble.
Phishing Attack Prevention and Ways to Identify and Avoid Scams
October 28, 2024
Comments are closed.
-
Why is heart rate reserve more accurate?
October 25, 2023